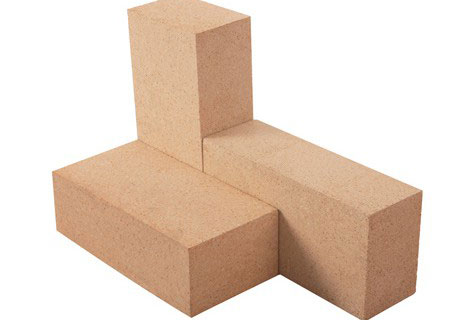
In situations which can be less harsh like natural gas or electric fired kilns, the kiln bricks which are more porous would be the preferred choice. These bricks are weaker, yet far lighter along with more straightforward to form. Additionally, they insulate a lot better as compared to the dense bricks. Either way the firebricks will not spall, while their strength usually holds up very well through the rapid changes in temperature that happen to be common within these applications.
The Manufacturing Processes
When creating https://rsrefractoryfirebrick.com/fire-clay-bricks-for-sale/, the fireclay is first fired in a kiln until it becomes partly vitrified. For the specialized purposes they are often glazed. Both the sizes that are standard to the fire-brick is definitely the 229x114x76mm and the other 229x114x64mm. These bricks can also be presented in what is known firebrick splits that have ½ the thickness that are frequently used for lining fireplace inserts and wood stoves. Proportions of the split bricks is often 229x114x32mm. The firebrick was invented around 1822 by William Weston Young.
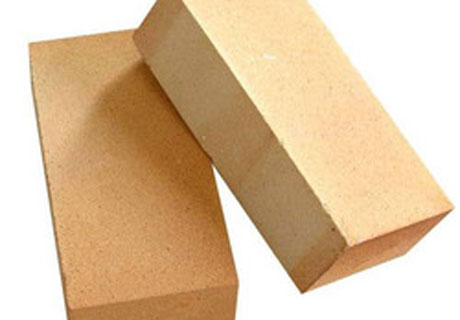
High Temperature Applications
Silica firebricks which are utilized to line the steel-making furnaces can withstand temperatures of up to 3000°F, that would usually melt most ceramic type materials. HRSI (High-Temperature Reusable Surface Insulation) and that is a material that shares the identical make-up was adopted to insulate tiles on the Space Shuttle.
The non-ferrous metallurgical processes make use of basic refractory-bricks as the slags used over these processes dissolve the “acidic” silica bricks readily. The more common refractory bricks that are used during smelting non-ferrous metal-concentrates can be the magnesite-chrome of chrome-magnesite bricks.
Lower Temperature Applications
There are a selection of other material types which are used by means of firebricks to the lower-temperature applications. The magnesium oxide bricks are definitely more commonly used for linings in furnaces. The silica bricks can be a common brick type which is employed in inner linings of incinerators and furnaces. For the reason that inner linings are usually of the sacrificial nature, the fire brick which has alumina content which is higher is normally accustomed to extend the duration involving the re-linings.
In most cases cracks become visible within these sacrificial inner linings soon after they are placed into operation. Silicon carbide, that has a higher abrasive strength, is one of the more popular materials to the hearths inside incinerators in addition to cremators. The red-clay bricks that are extremely common are being used more in applications for example wood-fired ovens and chimneys. Learn more from https://rsrefractoryfirebrick.com.
No comments:
Post a Comment